DME Cooling Solutions
Providing greater thermal control for today’s molding industry. Optimal heat and cooling is key to the economics and quality of a plastic part. DME cooling solutions include Analytical/Design Services, 3D Additive Conformal, Flow Control, Cooling Channel Maintenance and Temperature Controllers.
Featuring
DME Cooling Program
Increase profit by optimizing your tool with DME’s 5-Step Advanced Cooling Program.
"COOL" Savings
Numbers don’t lie. DME TruCool can save you money.
Optimized FLOW
Maintain consistent part output with DME Flow Technologies.
For More Information
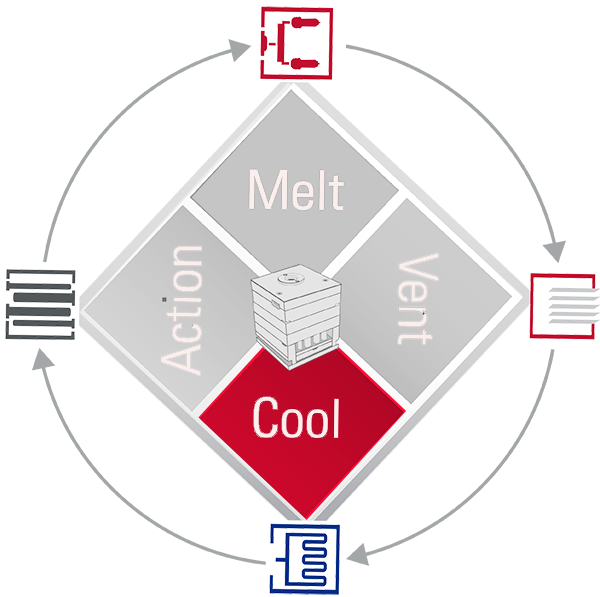
MOLD COOLING OPTIMIZATION
DME brings unique benefits to mold cooling at the time of DESIGN and throughout the entire molding PROCESS.
DESIGN: optimal performance of the tool relies on a thorough analysis and integration of superior cooling solution at the point of design.
PROCESSING: the performance of even best designed mold can be compromised without appropriate processing measures being taken. Control and monitoring of turbulent flow and channel balance over the lifetime of the tool are key to the mold’s efficiency and the ultimate output that can be achieved.
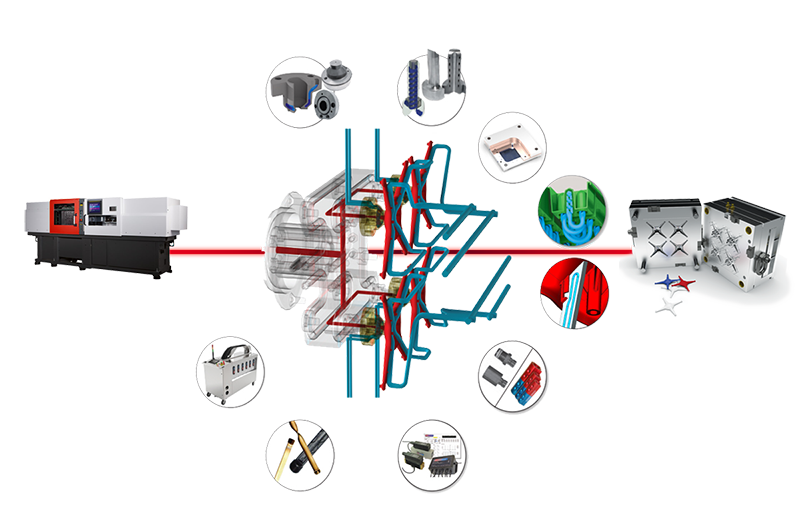
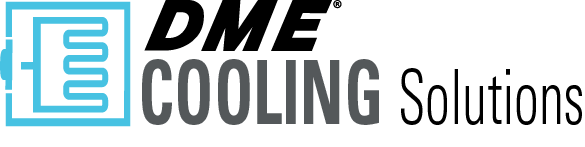
Boost Output
& Save!
Technology to Increase Production Output of High Quality Parts
√ Decrease Cycle Time
√ Improve Part Quality / Reduce Scrap
√ Greater Utilization of Assets
DME Cooling Solution & Cycle Time Advantage
One of the last elements of the mold design process, the cooling of the mold is rarely optimized and provides major opportunities for improvement. DME offers a breadth of technology solutions to better cool the mold, maintaining part quality and extending tool life.
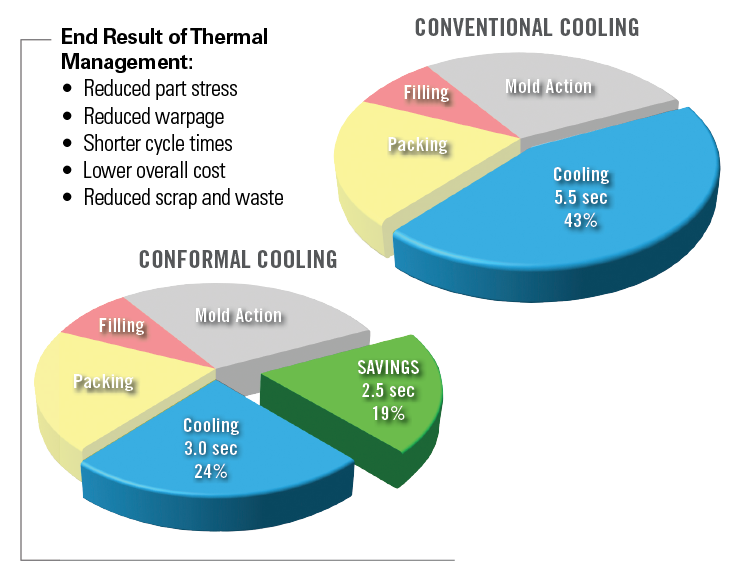
Cooling often is the largest portion of the molding process, opening the door for significant improvements and savings. Click below to see how DME’s Cooling Technologies can help optimize the thermal management of your next project.
The result is a faster cycle time and reduction in part defects increasing the output of high-quality part.
TIME - Your Most Valuable Commodity
Maximized Efficiency = Maximum Output
The DME 5-Step Cooling Program brings together DME’s vast array of thermal management products and technologies to reduce cycle times and improve part quality.
With advanced design, cooling channel location, proper flow / turbulence control, and maintaining continuous lifecycle performance through aftermarket parts and services; DME can help you maximize profitability over the lifecycle of the tool.
Mold Productivity Lifecycle


CASE STUDY IN SAVINGS:
The manufacture of a soup bowl required 3 tools running in 3 presses to produce 125 million parts per year.
New orders pushed demand to 175 million parts per year.
Attempts to simply increase output by reducing cycle time failed, increasing scrap to unacceptable levels due to warping. The only solution appeared to be the purchase of 2 new molds and the adding of 2 new presses to the facility, a very expensive proposition.
Presented with this challenge, the DME Engineering Team, using DMEs expertise in Mold Flow and FEM, identified a different approach. By deploying DME’s TruCool Conformal Cooling inserts, using the latest in 3D additive technology, the molder client was able to boost output by 35% while reducing historical scrap rates.
The result: NO additional investment was required, and the extra 50 million parts were shipped on time.
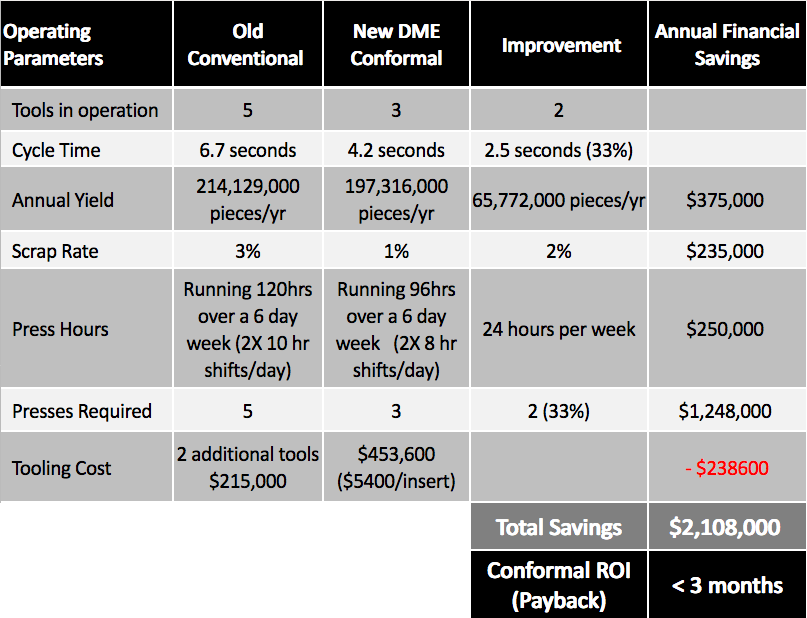
DME 5-Step Cooling Process

STEP 1: Design Optimization
DESIGN OPTIMIZATION: Determining the cooling required in a mold is typically the very last step of the mold designers process. Consequently, the cooling performance is often sub-optimal. This can cause unnecessary long cycle times and high scrap rates in the molding of the plastic part. By investing in the upfront analysis into your mold, you will avoid troubles such as gate resizing, runner enlargements, cooling alterations and much more. This leads to a greater return from your mold.
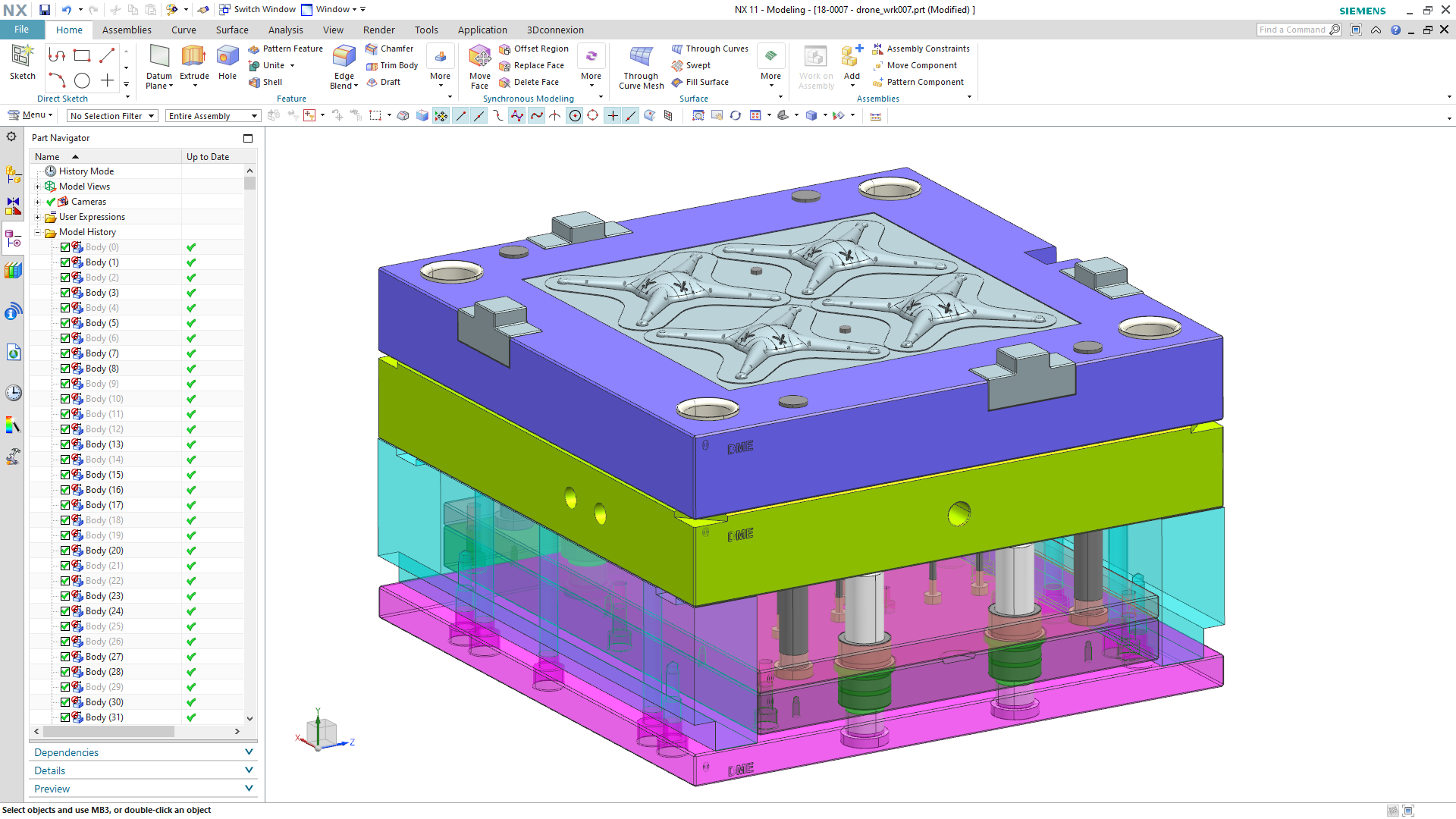
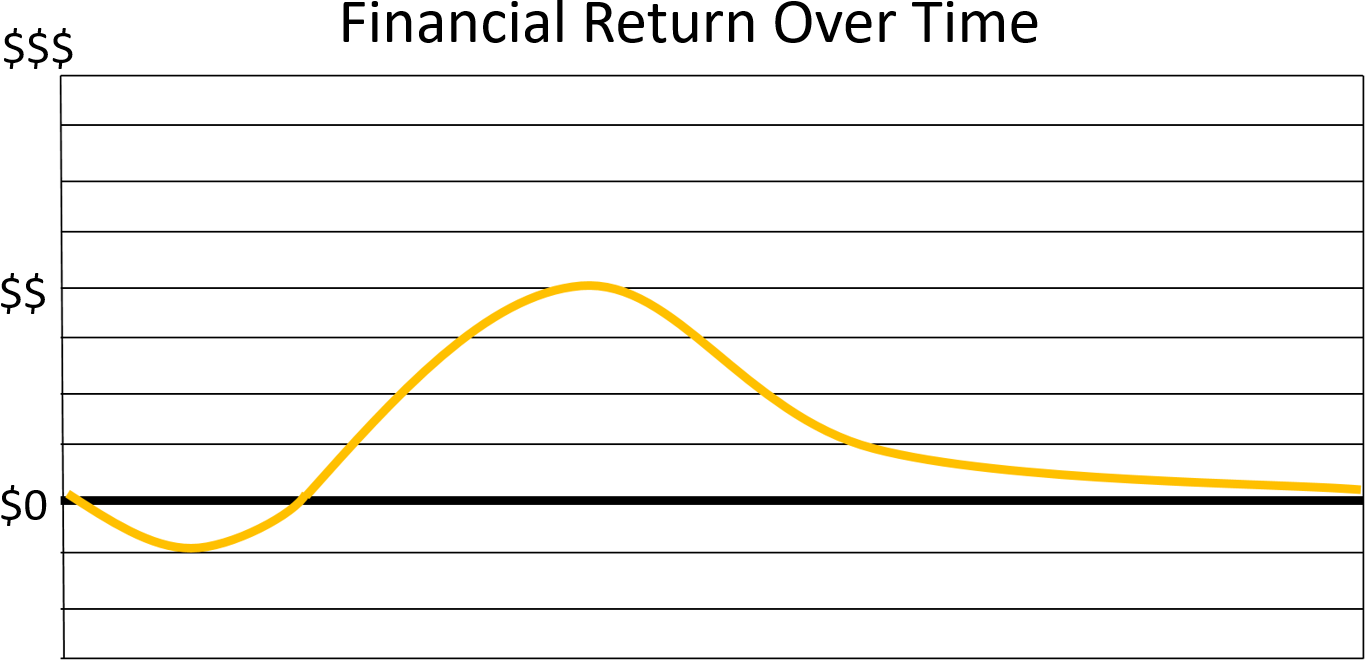
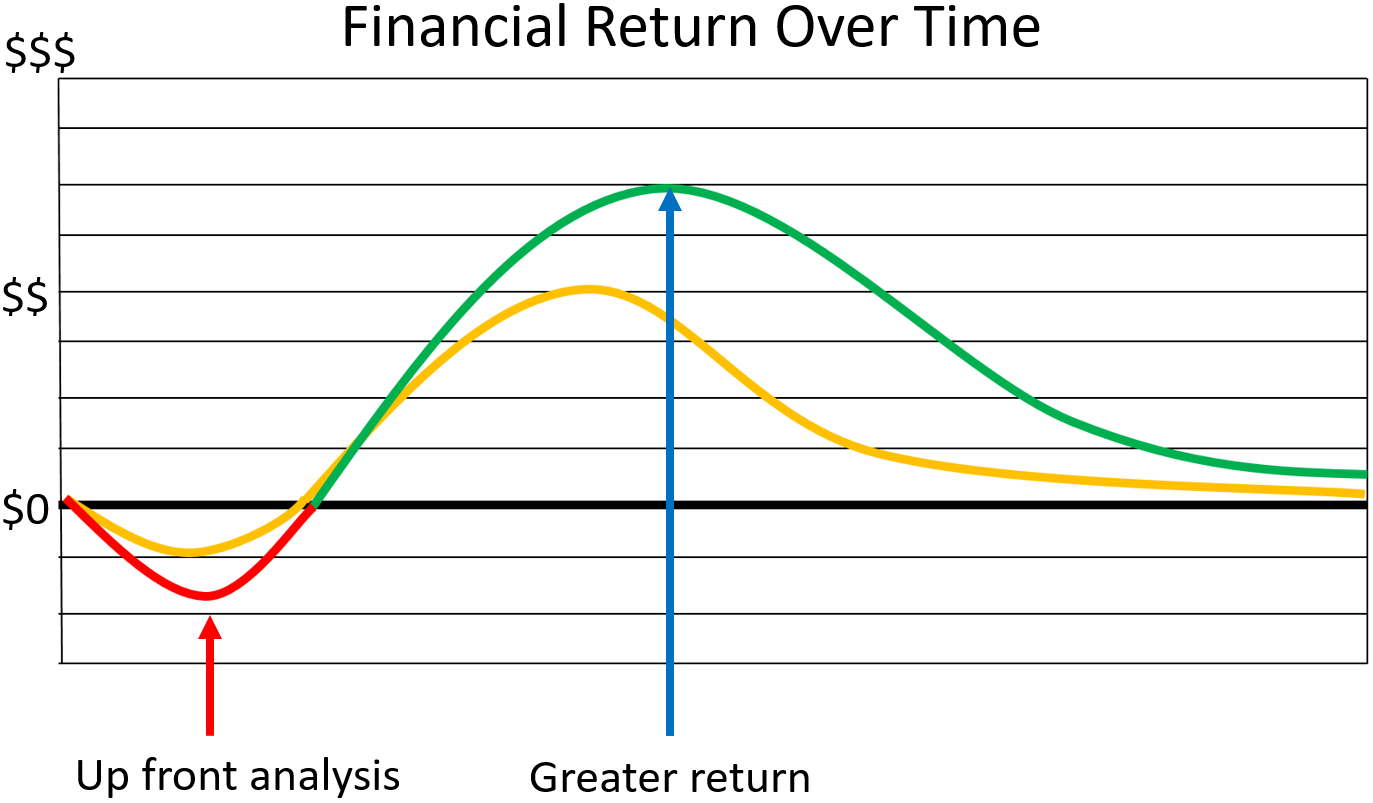
DME offers analysis and design services as well as a portfolio of mold technology products that can optimize the performance of the mold design. Specifically, by using DME’s mold cooling technologies, cycle times can be reduced by on average 20%, boosting the productivity of any molding operations.
For more information on DME Design Services Click Here.
DME Whitepaper
The benefits of undertaking computational fluid dynamic analysis prior to mold cooling design and manufacture.
Optimized cooling is crucial to an injection mold’s performance and much light has been shed on the matter in recent years. With the addition of conformal cooling and advanced strategic design we able to greatly improve the productivity of a molding process, the quality of the manufactured part, and life expectancy of the mold. To download the full whitepaper click the button below.
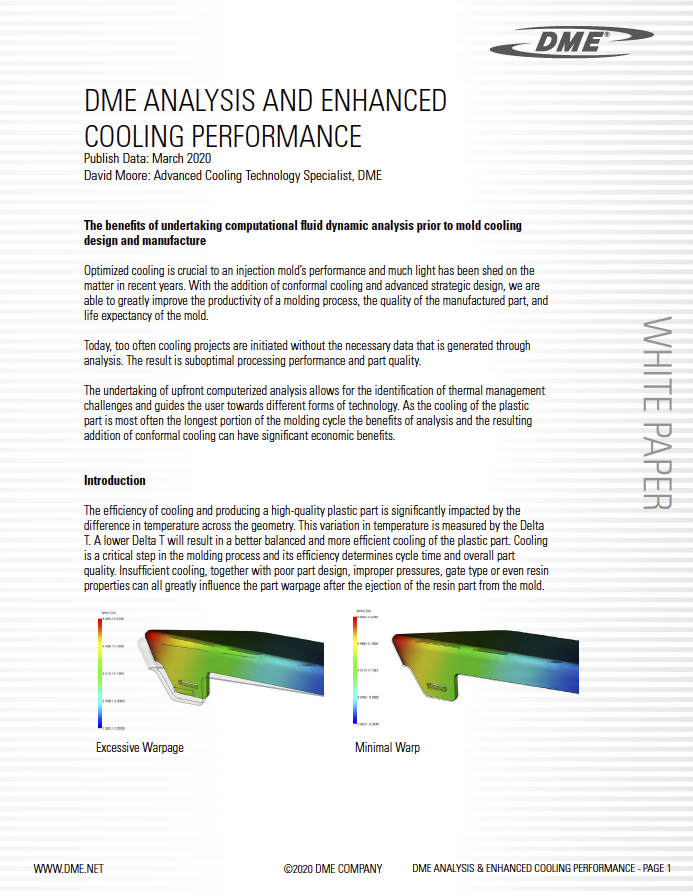
DESIGN TIP:
The Importance of Proximity
The geometry of the part greatly determines the complexity of the cooling process. The objective is to position the cooling media in the correct proximity to the mold surface and plastic part. Too close and you run the risk of premature cooling which may result in short shots and poor part quality. If too far from the surface, then cycle times and potential warpage become an issue. The use of our Analysis Services can help with defining the strategic placement of the cooling channels.
When conventional water channels are unable to reach into certain areas, residual heat builds up. This results in the need to slow the molding process and delay ejection.
However, by optimizing cooling through the selection of one of the DME TruCool conformal cooling technology’s, we can cool difficult to reach areas and manage the temperature delta across the part.
DME offers a range of different conformal cooling technologies each designed to meet your precise application requirements.
For your next project contact DME, Click Here to download request form.
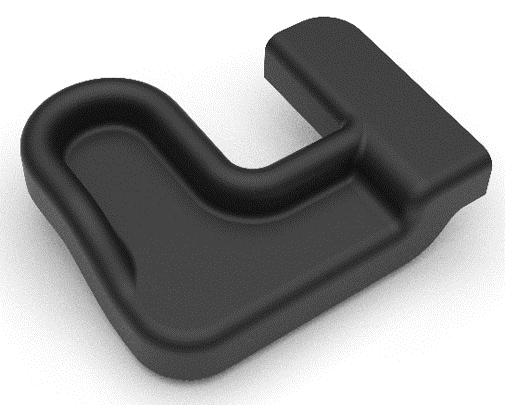
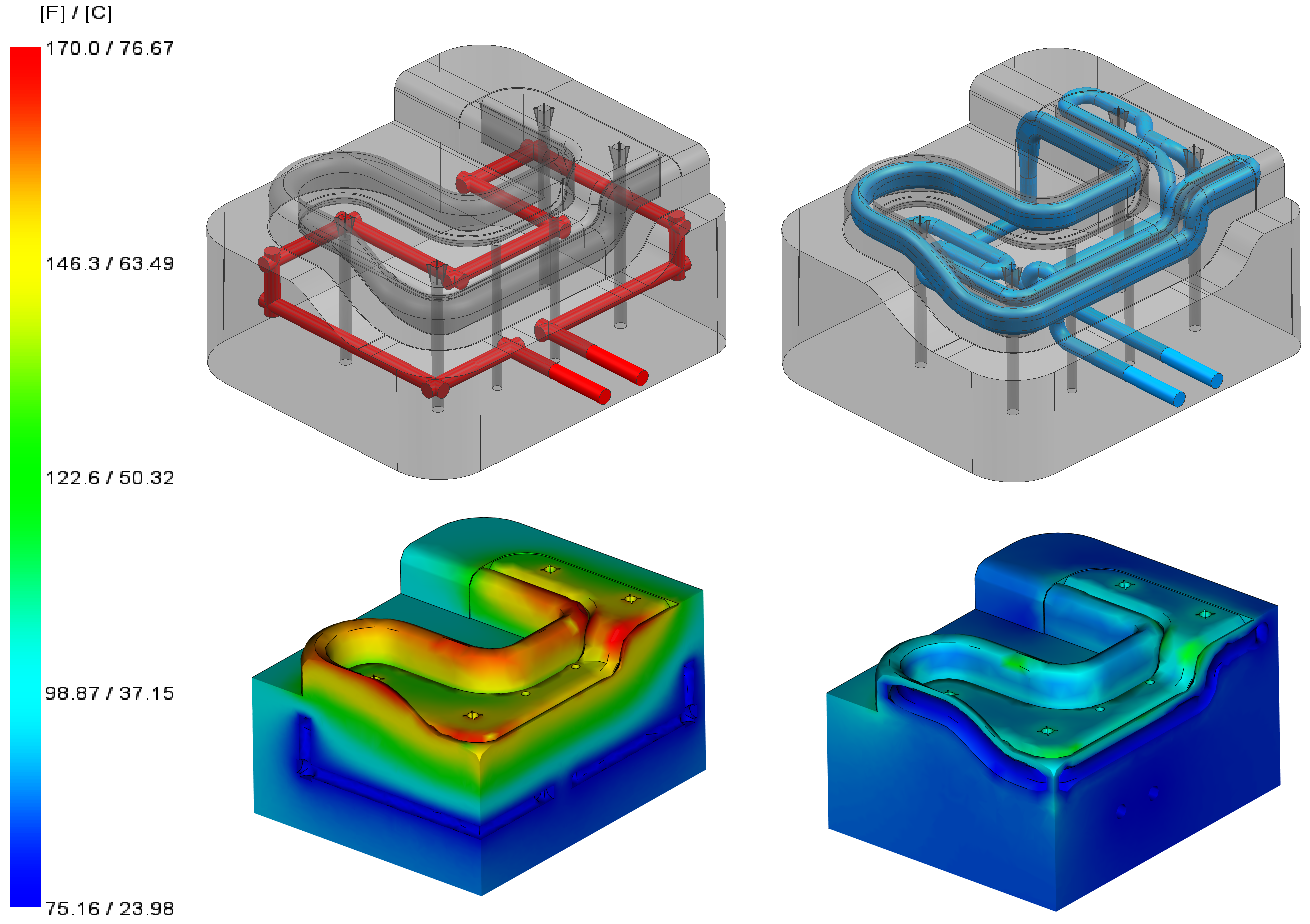
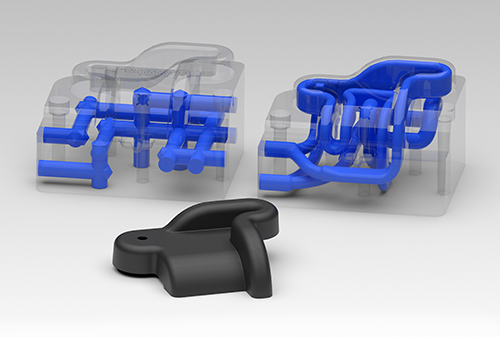
DESIGN TIP:
Class-Leading Aesthetics
The appearance of a product can be critical to its brand image. The automotive industry is such an example, where the lighting systems have become as much cosmetic as they are functional. In fact, all consumer products today rely on their design with perfect cosmetic appearance being key.
A common problem in the manufacture of a perfect cosmetic part is the generation of splay or blush at the point of the gate. This can result from insufficient cooling of the resin leaving the nozzle and entering the tool. This presents a dilemma, as the resin needs to be sufficiently molten to fill the cavity and core, but the heat profile needs to be controlled to avoid excessive heat which can cause burning, splay or blemishes. This is not always possible using conventional hot runner nozzles. The solution lies in the use of the DME conformal gate bushings available for hot runners. Uniquely designed, with a small footprint for space consideration, the DME product brings greater control of the molten resin allowing the molder to run at higher speed without the risk of poor part quality and delivering the perfect jewel!!!
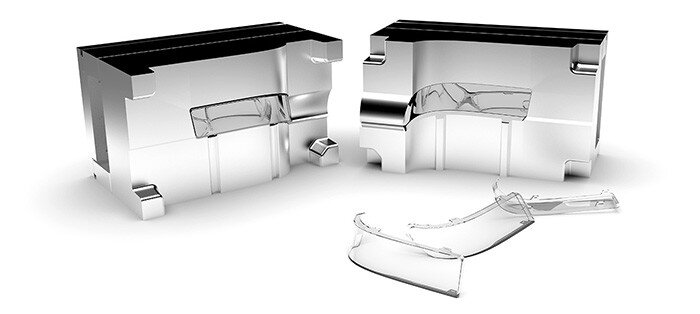
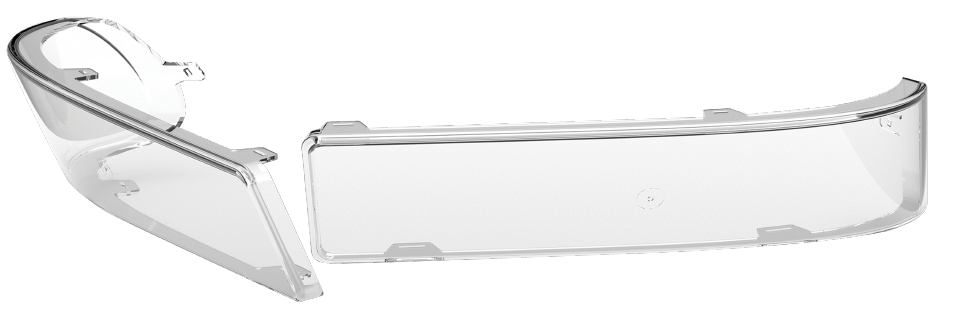
STEP 2: Cooling Technologies
DME provides advanced cooling tailored to your specific needs with a wide range of leading technology offering the most flexibility in the industry.
Understanding advantages of different manufacturing methods ensures the most effective solution for each individual project. From gun drilled channels in our mold bases, multi-piece brazing or diffusion bonding for more advanced cooling or 3D printing, diffusion bonding, MIM (Metal Injection Molding) and DED (Direct Energy Deposition) processes for highly engineered geometries, DME has the answer to your exact need.
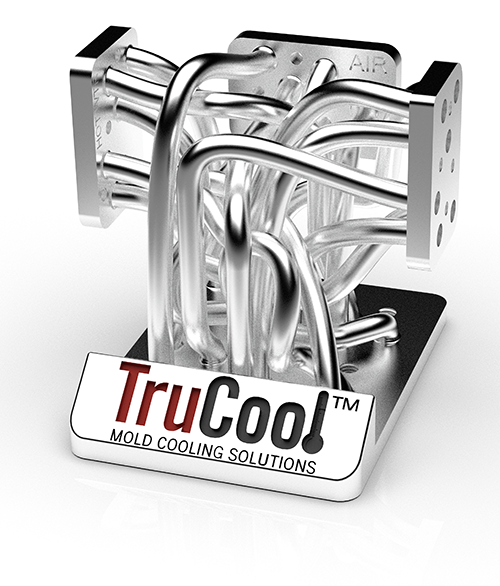
STEP 3: DME Flow Monitoring & Regulation
Optimized Processing – Controlling Flow & Turbulence
Processing
- PROCESSING OPTIMIZATION: Careful control of the water flow temperature and turbulence helps ensure the heat of the processed resin is efficiently and evenly transferred from the surface of the mold cavity.
- Ensuring turbulent flow becomes even more challenging the longer the mold runs. The corrosion of channels and build-up of scale restricts the flow in the cooling channels. DME provides turnkey solutions to rectify to maximize the molders manufacturing output increasing the profitability of the operation.
Reduce cycle time, improve part quality, reduce production downtime and lower energy/water consumption
Without careful management of water flow and turbulence molding performance will be sub-optimized
Water flowing straight through a channel without turbulence is referred to as laminar flow. This is a problem as water is confined to the surface of the cooling channel absorbing heat and preventing heat from being efficiently transferred and carried away from the surface of the mold. Simply adding more water flow is not the answer and leads to unnecessary use of energy and water. It can also create an excessive draw on the water delivery system being used by other presses and further reducing the mold cooling performance. Turbulent flow is the solution. Turbulent flow circulates the water within the channel maximizing the transfer of heat away from the tool to the water flowing through the channels and thus improving cooling efficiency.
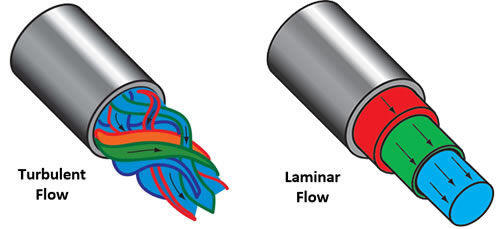
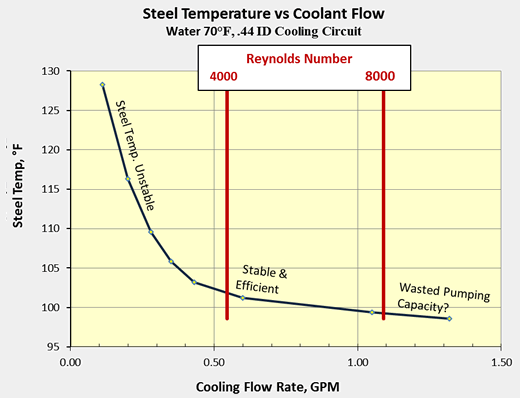
Measuring TURBULENT FLOW
The Reynolds value is used to mathematically measure the turbulence and flow and has been the basis of measuring turbulence for generations. A low Reynolds value means laminar flow while a high Reynolds number means turbulent flow. Too much turbulence is a waste as it requires exponentially more energy to push the coolant where minimal gain is achieved. The optimal Reynolds value, between 4000 and 8000, can be controlled using the DME Smartflow® flowmeter (View on eSTORE) or where a digital solution is preferred, the TraceVM Base (View on eSTORE)
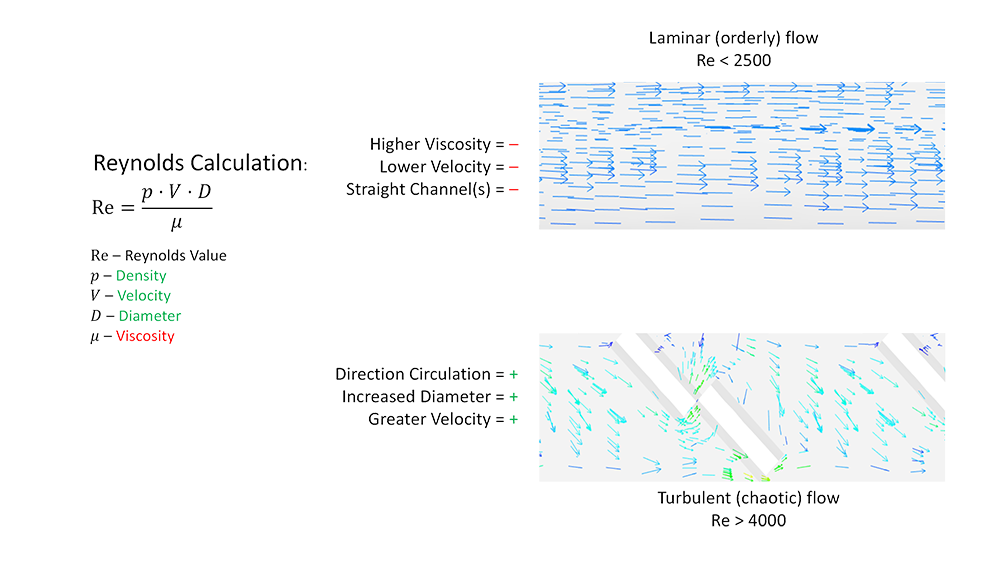
STEP4: Lifecycle Performance
Maintaining cooling performance over the life of the tool is key to achieving maximum output.
Over time the water channels are prone to scale build up and rust both of which negatively impact turbulent flow and heat transfer. The restriction of flow and the insulation properties of scale will result in irregular cooling of the tool increasing the Delta T. Therefore, to avoid part quality problems, the manufacturing process will typically need to slow the process to accommodate the cooling requirements prior to ejection of the part. The good news is that this sub-optimal performance can be avoided by a Preventative Maintenance program that uses the DME CoolingCare System.
The DME CoolingCare System cleans the lines restoring them to their original levels. The advanced capabilities of the CoolingCare product enable unattended operations benefiting from Industry 4.0 connectivity to signal to the operator when the cleaning is complete.
To learn more about CoolingCare Click Here.
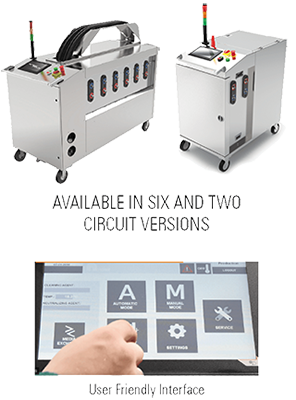
STEP 5: Digital Connectivity & Industry 4.0
Taking control to the next level DME is actively involved in Industry 4.0, building intelligent connectivity between equipment processors. The result is a smart system providing visibility in real time to measure and control performance of the operations. The benefits include improved quality, reduced down time, managing operations proactively, react quickly to problems, predictive maintenance and provides secure/private audit trails and reports.
Controlling all of the different parameters influencing the thermal management process is key.
DME deploys a wide range of controllers to meet your requirements.
The Smart Series® Me hot runner control system brings advanced, and exclusive features to the realm of hot runner temperature control. Designed to increase processing efficiency, the Me’s advanced operator interface will decrease set-up time and provide operators with exclusive tools to efficiently and effectively troubleshoot and make process changes.
Learn More about Me Temperature Controllers
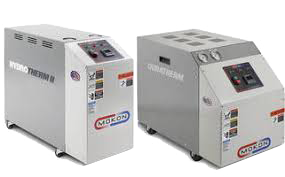
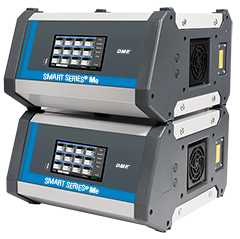
Meeting the technological and operational needs of today’s every changing digital environment.
- Improve quality
- Reduce down-times
- Manage operations proactively
- React quickly to problems
- Secure + private
- Audit trails + reporting
- Path to predictive
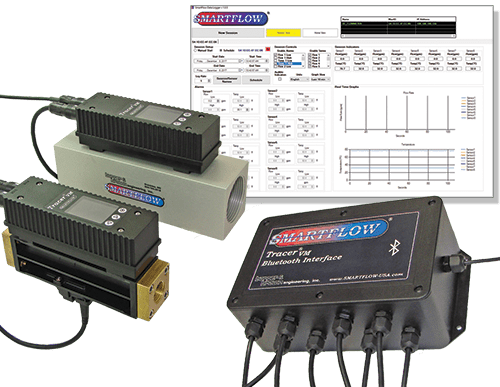
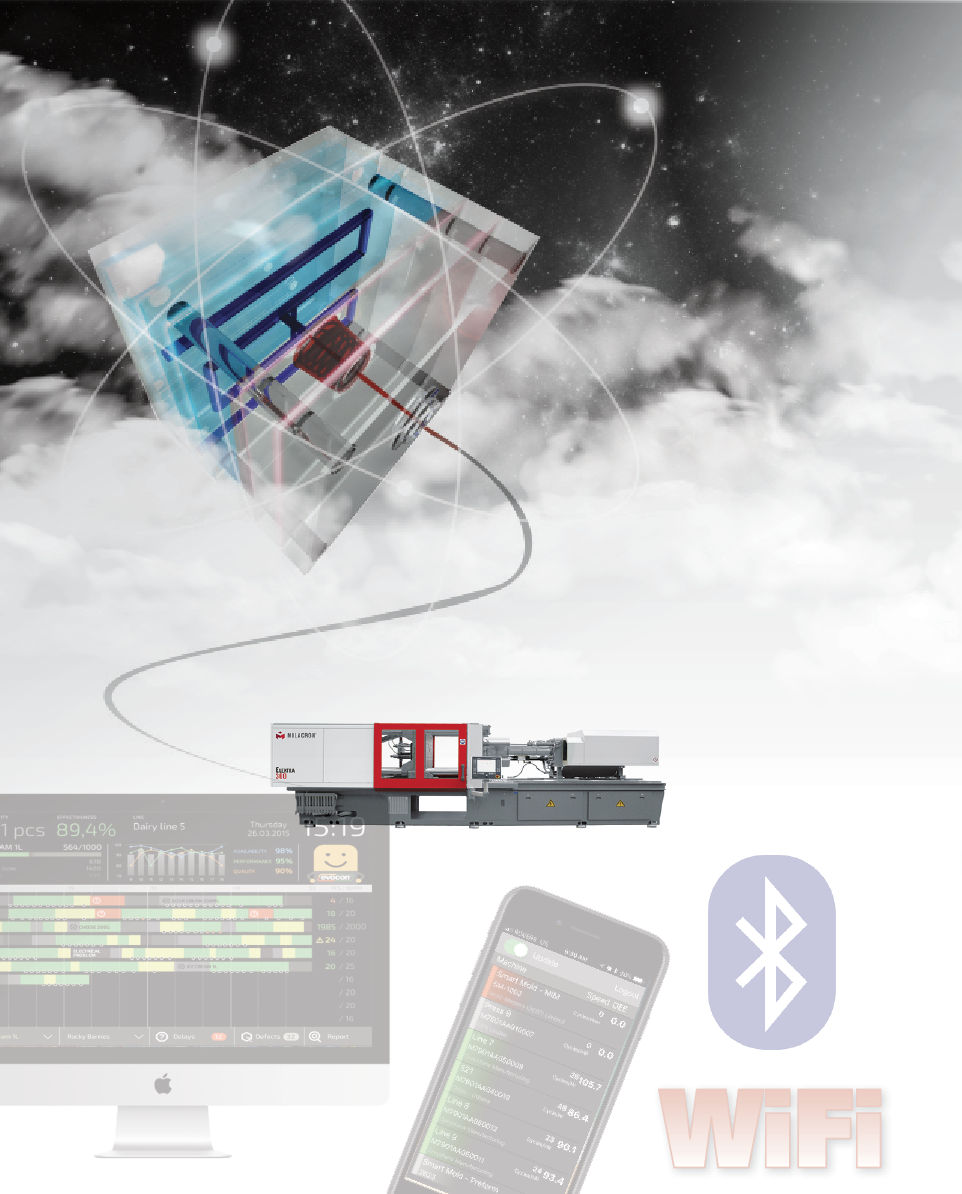